Advanced Features
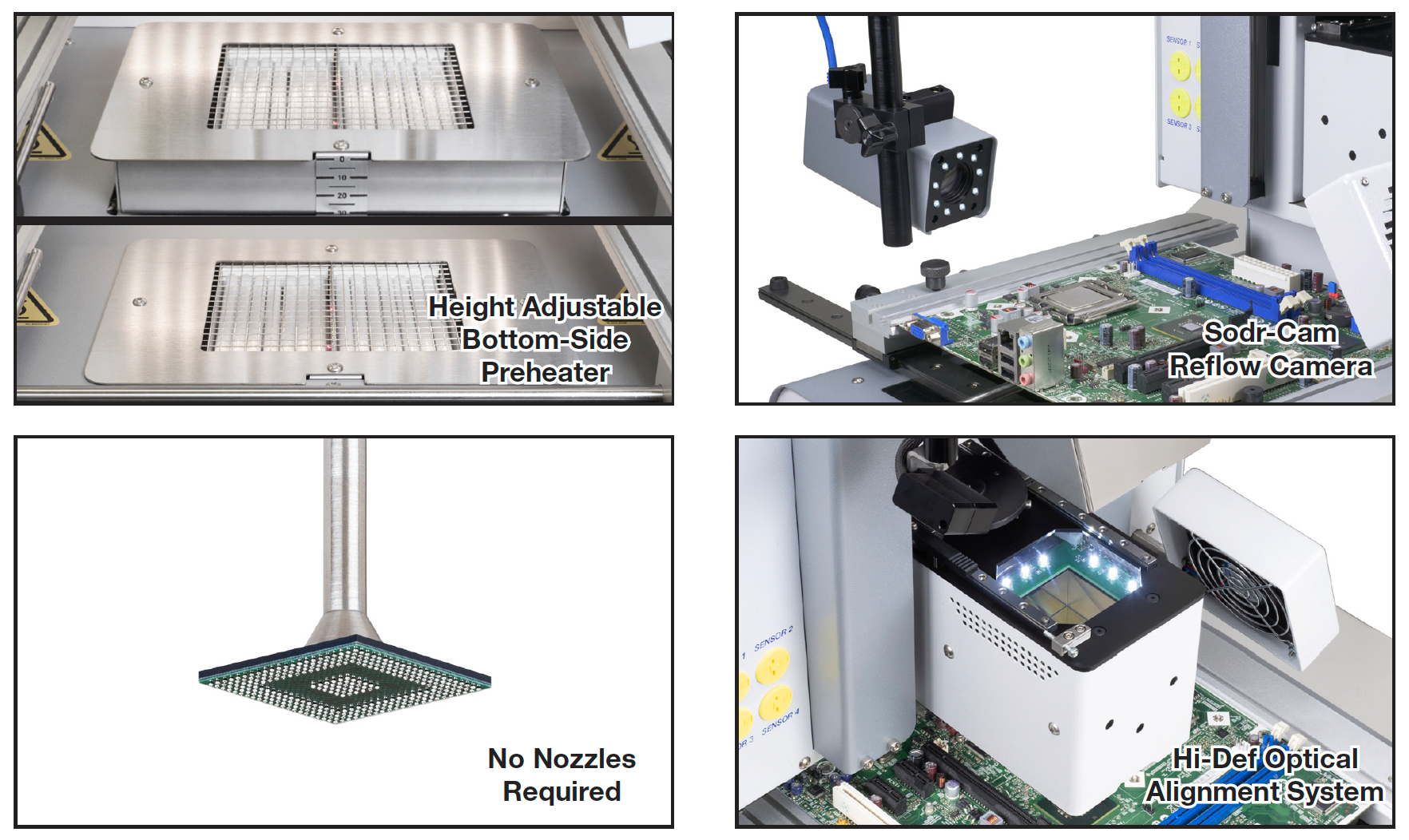
• Ultra-High Precision Placement Capability: Motorized reflow head is driven by advanced stepper motor system providing smooth, high precision, repeatable movement with no drift, allowing for soft landing of components and 28μm (.0011") placement accuracy.
• High Sensitivity Vacuum Pick: New Vacuum Pick design is more robust, utilizes an optical sensor, is counterweight balanced, and employs precision high-temperature linear ball bearings for maximum accuracy and sensitivity in placement and pick-up.
• Sodr-Cam Reflow Camera: Provided Sodr-Cam allows the operator to verify the entire reflow process, including the exact moment of solder melt.
• Height Adjustable Bottom-Side Preheater: High powered (1000W) IR preheater height is adjustable from standard position up to 38mm (1.5") closer to the PCB for the most challenging high-thermal -mass boards.
• High-Definition Optical Alignment System: Automated Vision Overlay System uses a beam-splitting prism, high intensity LEDs for shadow-free lighting and a new high definition 1080p camera for easy alignment.
• Quad-Field Imaging for Large/Fine Pitch BGA's: Allows up to four corners of a large component (and its lands) to be viewed under high magnification, providing perfect alignment of outsized BGAs or fine-pitch QFPs.
• Integrated Board Support Wand: Prevents warping or sagging during reflow, is extremely adjustable to clear parts on the bottom of PCB and is easily removed when not in use.
• Power Distribution Graph: Provides a graphical analysis of the top heater output within each zone, helping the developer make necessary adjustments to either the bottom heater utilization, or ramp rate, to maximize thermal performance.
• Sensor Offset: Allows the developer to easily match the pyrometer temperature reading to the actual solder temperature.
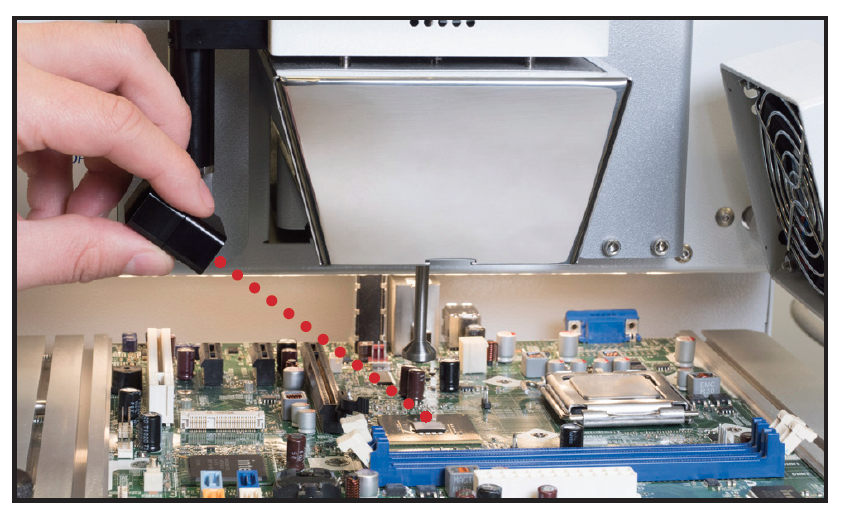
Non-Contact IR Pyrometer: A closed-loop, non-contact IR pyrometer monitors and controls the ramp-rate and temperature of the component in real time, by controlling the top and bottom heaters’ output throughout the heating process.